Plug & play motor retrofit project
5th December 2022
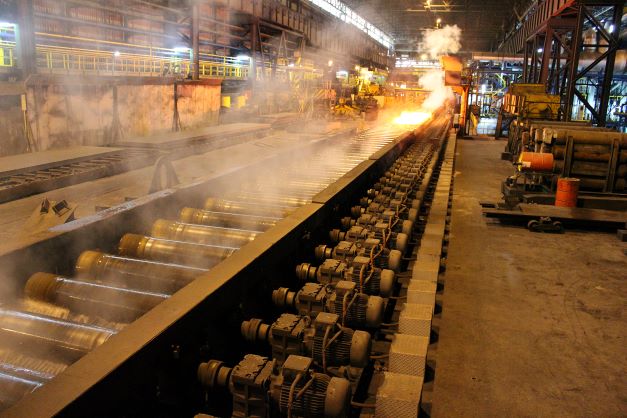
Carrying out a large scale retrofit at any facility can be daunting, but at a steel mill, where extreme conditions and high productivity demands combine, particularly so. As equipment such as motors require replacement, plant operators need to install new units quickly to safeguard uptime. That’s why Aperam, a leading producer of steel and alloy, selected Bauer Gear Motor to carry out a three-year retrofit project for the roller table conveyor drives at its Châtelet facility.
While the operating life of a motor can exceed 10 years, eventually plant managers will need to upgrade to a new efficiency standard or replace faulty units. However, the footprint and interfaces of new equipment will almost never match up to the original, which can make retrofitting a modern motor problematic. Complex mechanical adaptations to fit the new unit can be very time consuming. With demand and prices for steel and alloy through the roof, any extended downtime for a retrofit project at a steel mill must be avoided.
The Aperam Châtelet facility in Belgium consists of a melt shop and a rolling mill, which produces durable steel and alloy. During routine inspections, maintenance engineers at the plant identified that the motors powering the roller table conveyors required replacement. Due to the weight of the slab, each roller was powered by its own dedicated motor. Therefore, carrying out a motor retrofit project – which would require extensive mechanical adaptation for each unit – was unacceptable. Consequently, Aperam approached Bauer Gear Motor, a brand of Altra Industrial Motion Corp., to provide a plug and play motor retrofit solution.
Bauer retrofit solution
Bauer Gear Motor says it is a world leader in geared motor technologies, with a proven track record in providing highly robust and reliable drives for use in challenging metal industry applications. Focused on delivering motors that attain the highest efficiency standards, Bauer also offers operators in the metal industry a plug and play retrofit solution for drives operating on roller table conveyors.
The Bauer retrofit solution features two key elements. A standardised shaft connection using either a flange or coupling ensures increased ease and speed of installation. This is matched by a foot adaptor plate, which allows a one-to-one changeover between the old and new motor. A plug and play design eliminates the need for any costly, time consuming mechanical adaptations. Consequently, retrofitting new motors can be done with minimal downtime.
Plug & play solution
“What was key for the Aperam project was that we could offer a plug and play solution as a complete package, which was particularly important to engineers at the facility,” explains André, Regional Sales Manager, North Europe. “Our extensive engineering knowledge in the metals industry and the OEM support we could provide were also deciding factors. One of the primary challenges was to deliver the volume of motors required within the timeframes of the plant’s scheduled downtime, but our production capacity ensured we could achieve this. Over three years, we have updated all the motors on the roller table conveyors, bringing the system up to a new efficiency standard while also streamlining future maintenance and retrofit work.”
Bauer offers specialised motors specifically for roller table conveyors. With heavy duty fan or non-ventilated designs, the motors feature windings for delivering high torque, heavy duty gearbox housings and gear wheels, seals to withstand high temperatures and IP65 enclosures as standard.
By standardising the shaft connections and footplates for Aperam, Bauer was able to not only streamline the initial retrofit project, but all subsequent motor upgrades or replacements required for the roller table conveyors in future. This ensures that as the Châtelet facility moves to improve energy efficiency and boost reliability, these dual aims can be achieved while safeguarding production uptime.